Morizumi mounting
December 20, 2019
Ric from Wheel Fanatyk visited recently and wrote about it on his blog. He was interested in my Morizumi setup and maybe others will be too. I’ll leave a few notes and build photos here.
I started with a King stand for big drills or small mills. A few considerations led to this choice: not too heavy to move alone but heavy enough to resist tilting under use; not too expensive; and available locally. The same stand is sold under different names in different markets so searching by keyword may be helpful if you’re looking.
The default option would be to mount a spoke machine directly to the stand but that would be low for me especially with my thick anti-fatigue mat in front of the tool. I took a sheet of leftover pine, chopped it on the table saw and laminated pieces together to create a top with my desired lift. I took advantage of the laminated construction to insert T-nuts between layers — I matched them to existing holes in the stand letting me attach the top with bolts from inside. Having no exterior hardware makes the top an uninterrupted flat surface, which is helpful in terms of oil containment.
By mounting my spoke machine to the wooden top I only needed to drill one hole in the metal stand — for the spoke offcut chute. If you’re a casual cutter this step might be unnecessary but it’s important for a production shop. I bolted my spoke machine in place and traced exactly where the chute would go. I cut the chute in the wooden top, mounted it, and used the top itself as a drilling guide. The result: spoke scraps fall through the chute landing in a bucket accessed through the main door.
Cutting oil is critical but I didn’t want to fix a drip tray under the machine. To protect the wood I wrapped it with Formica countertop laminate. The process involves gluing pieces with contact cement and trimming the edges with a router. Formica is oil tolerant and lets me wipe away drips without hurting anything. In order to prevent oil from seeping beneath the spoke machine and draining through its attachment points, I put a bead of sealant around the spoke machine on its final installation.
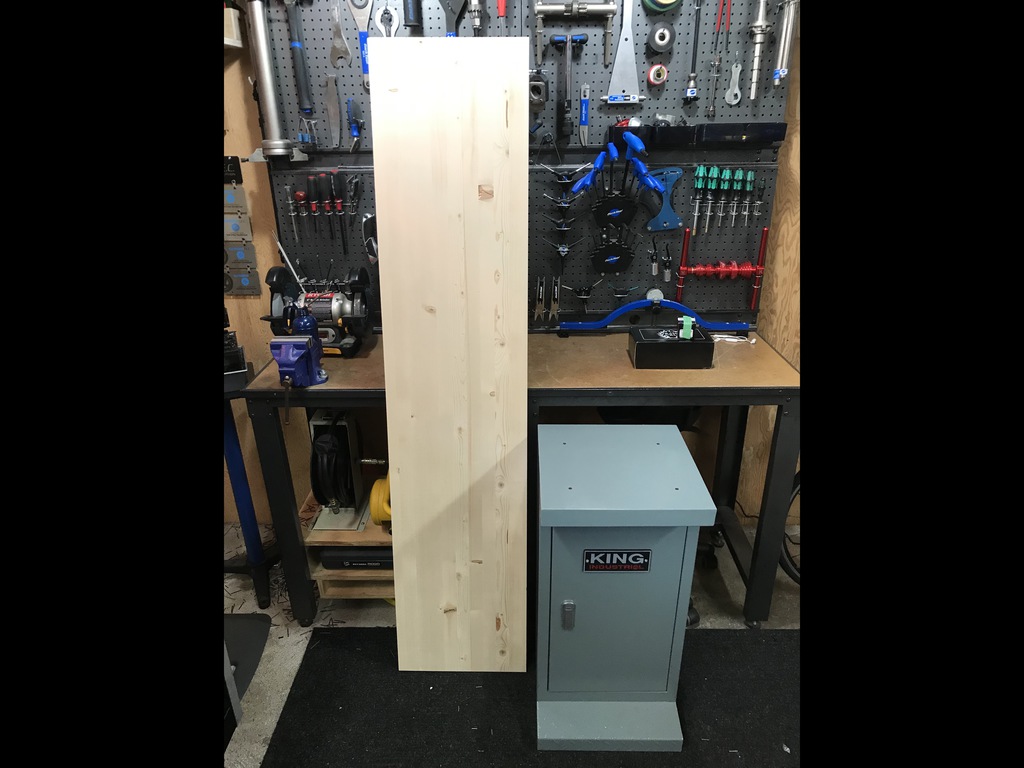
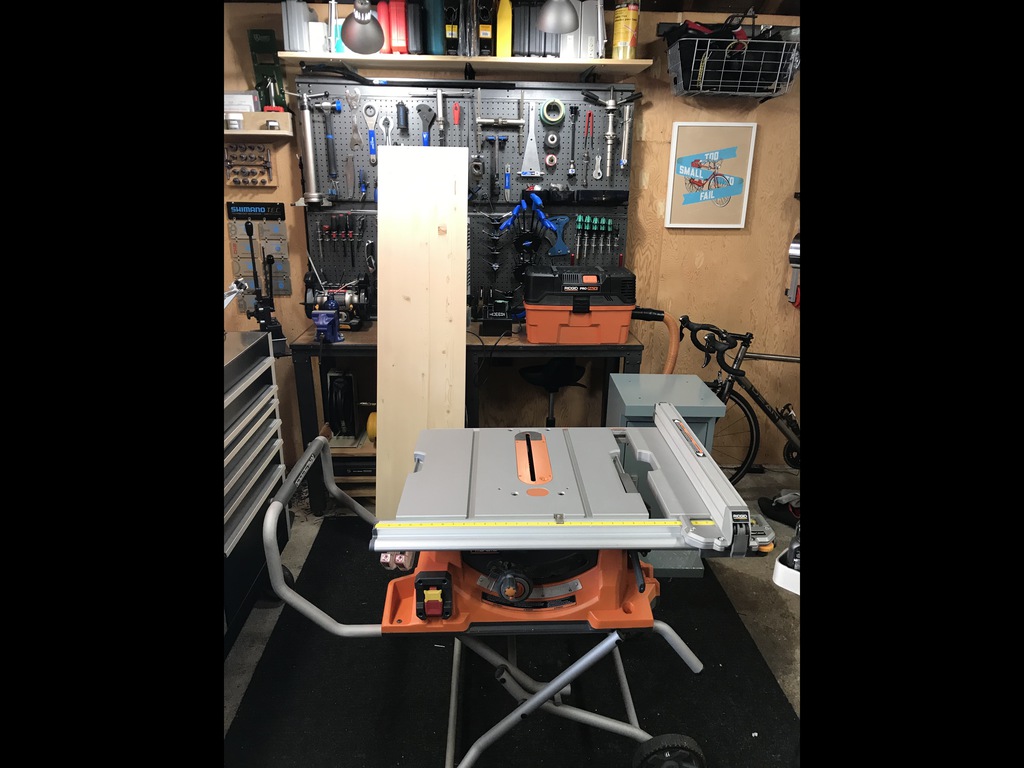
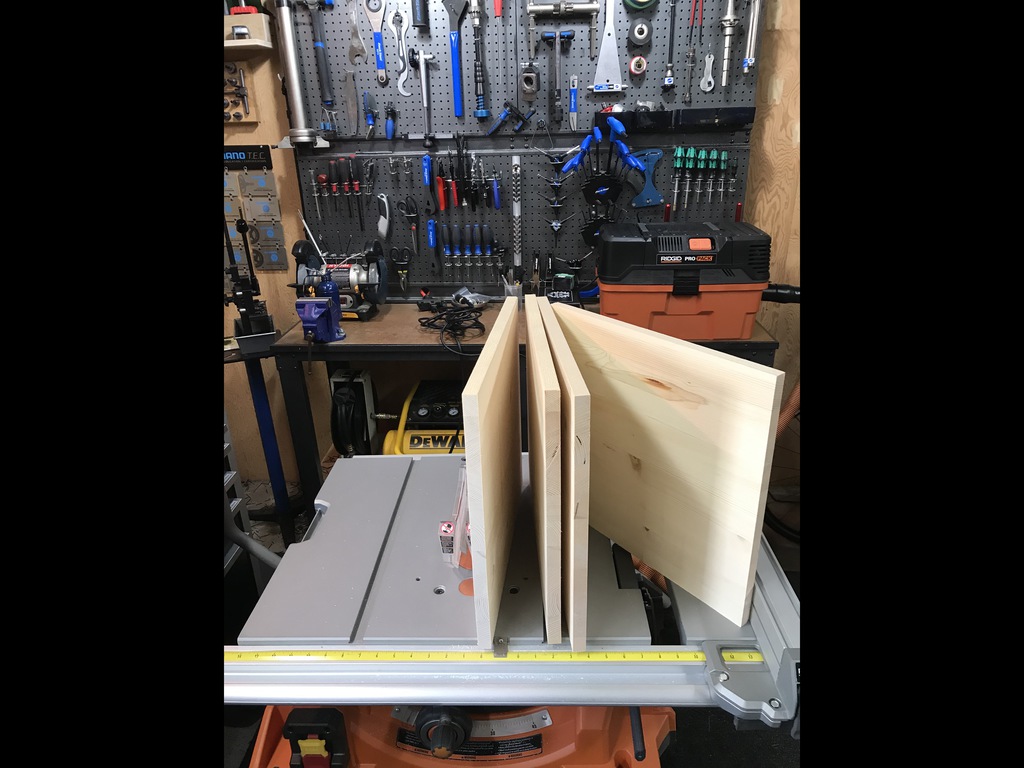
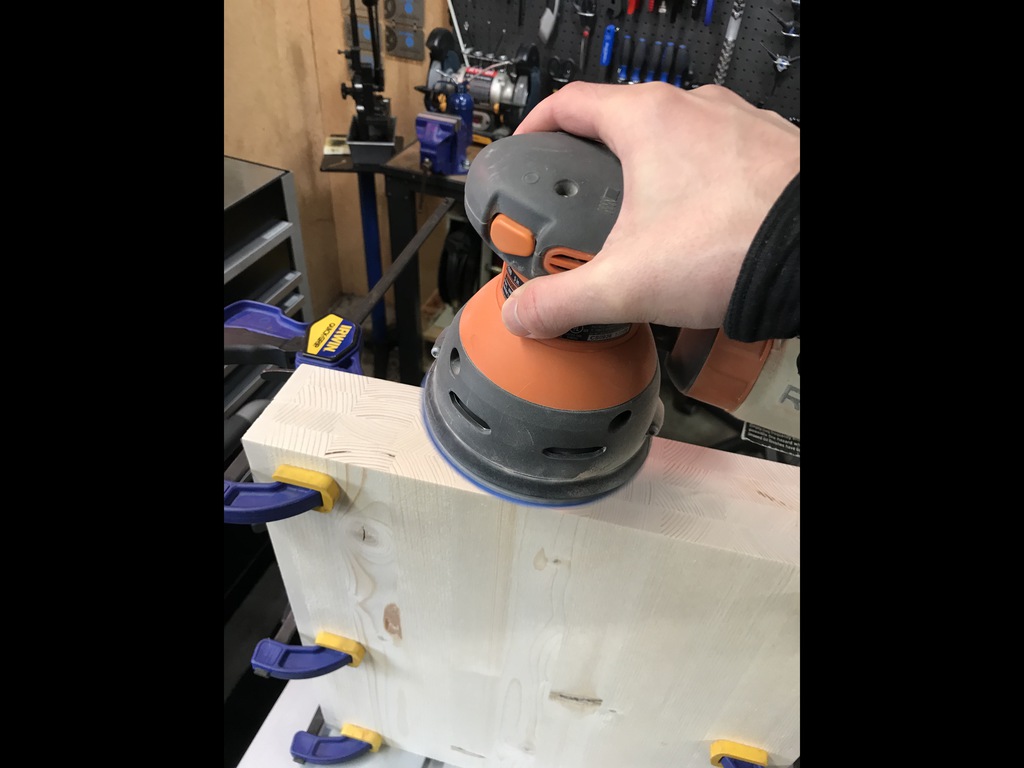
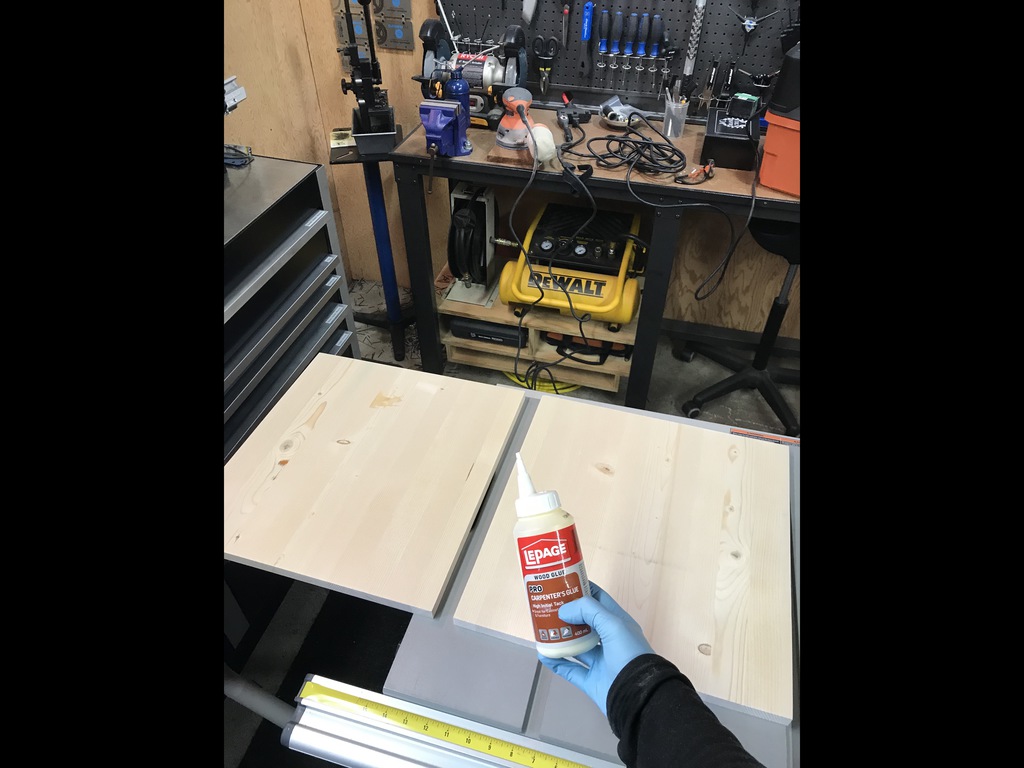
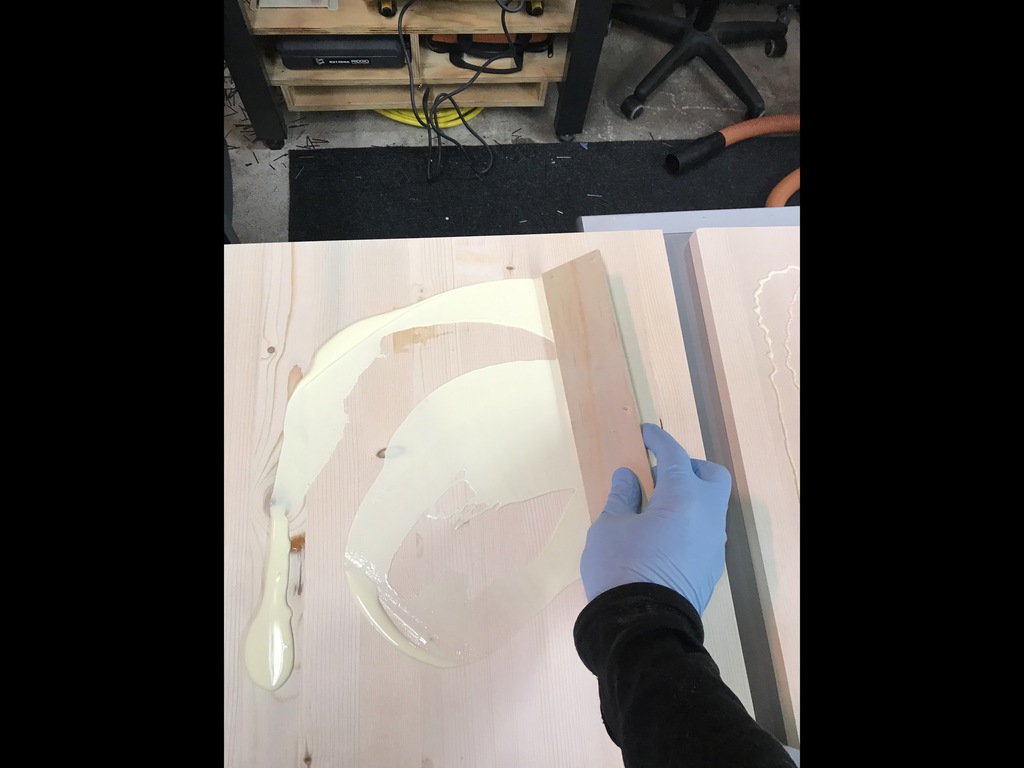
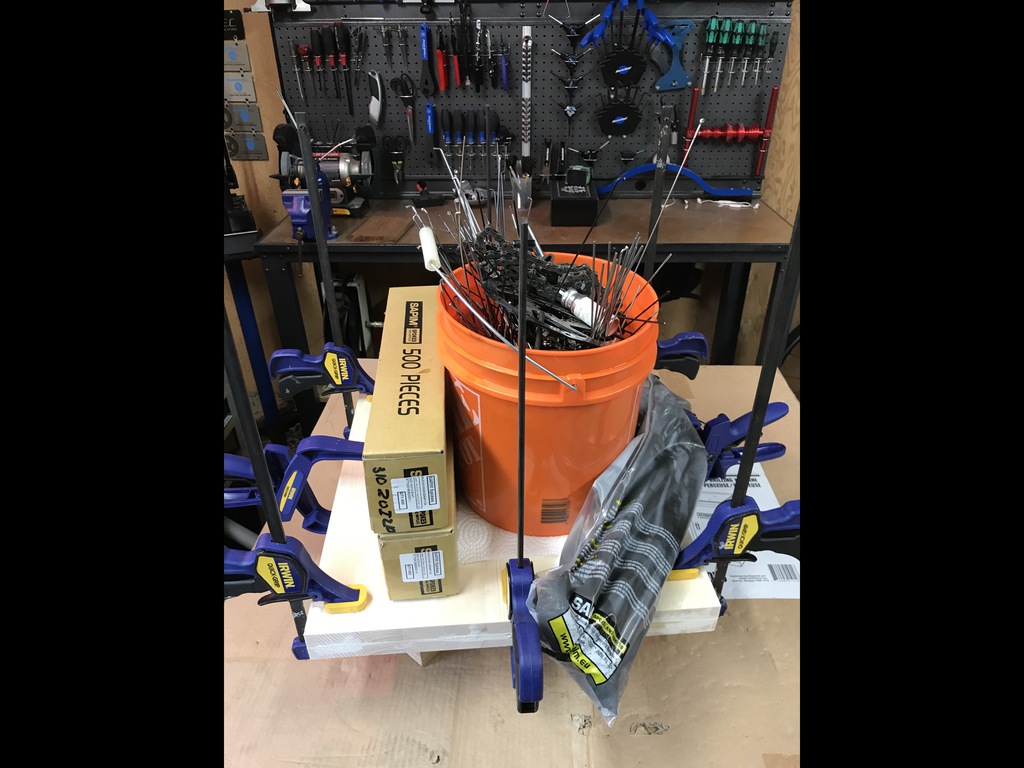
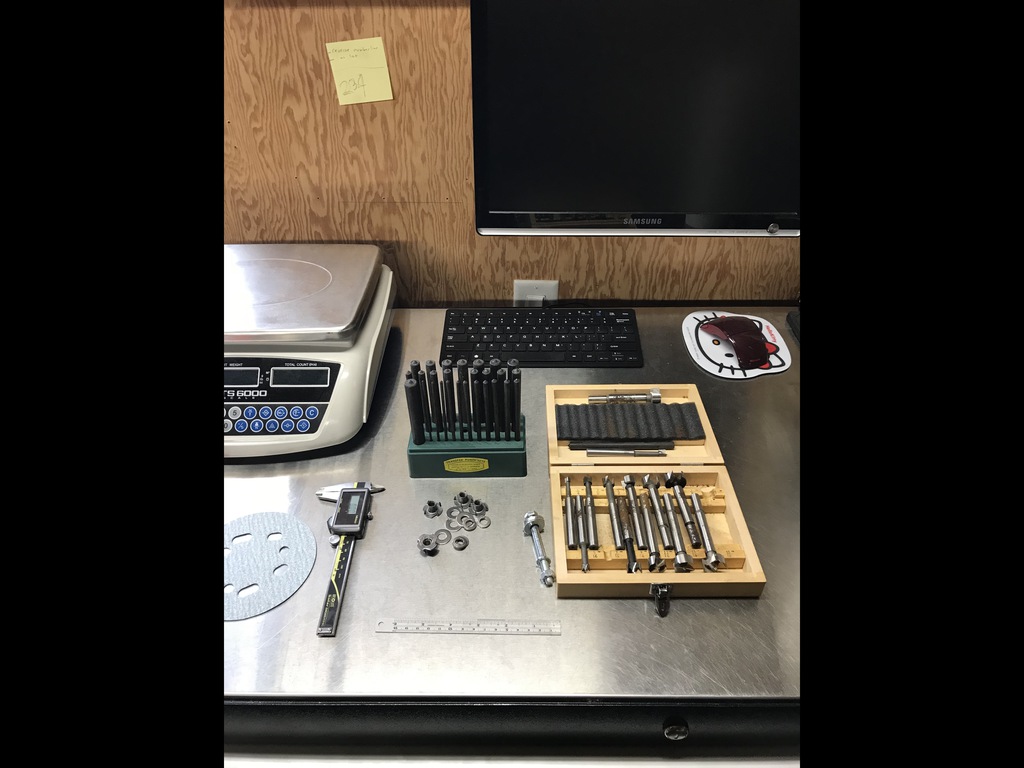
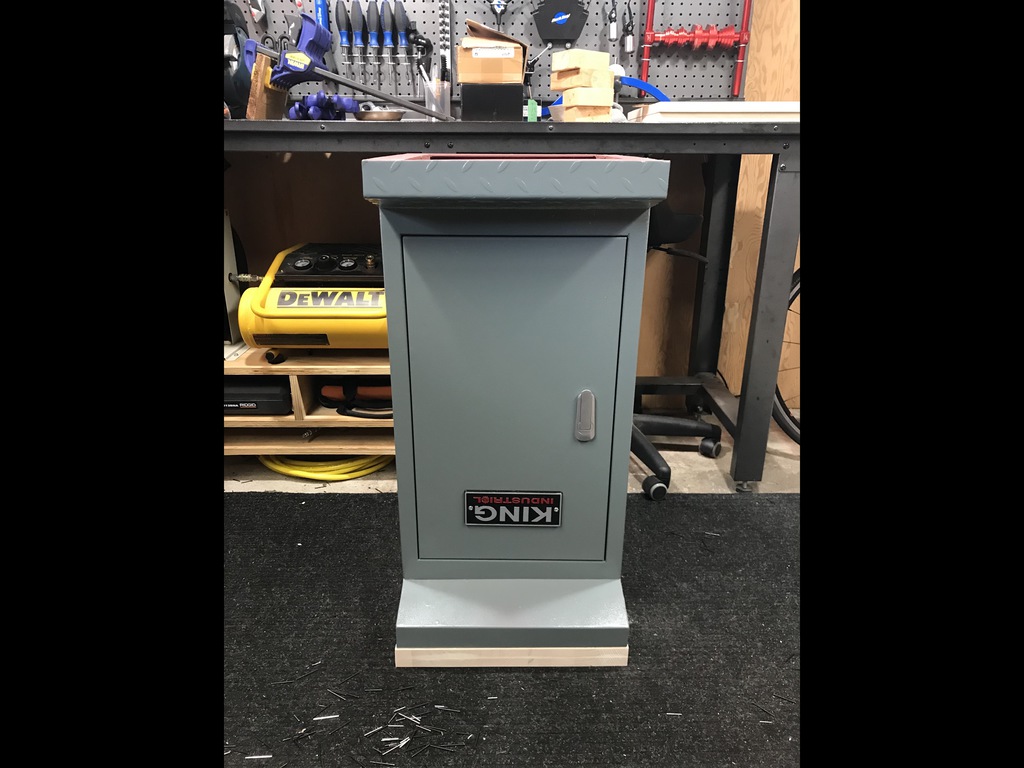
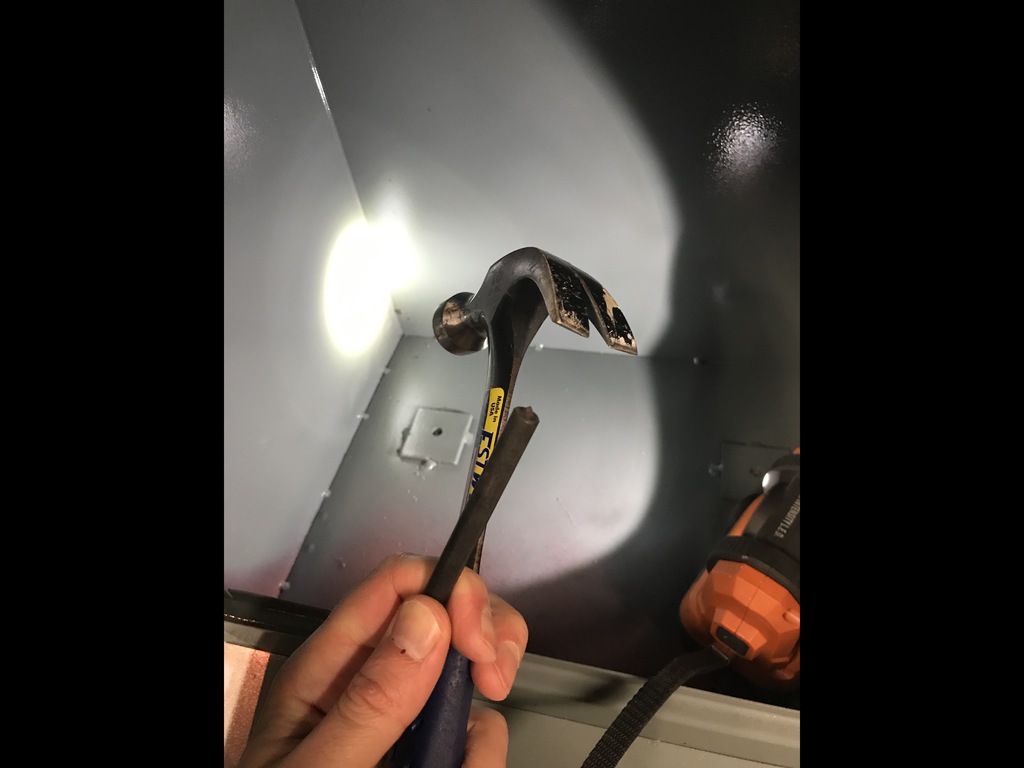
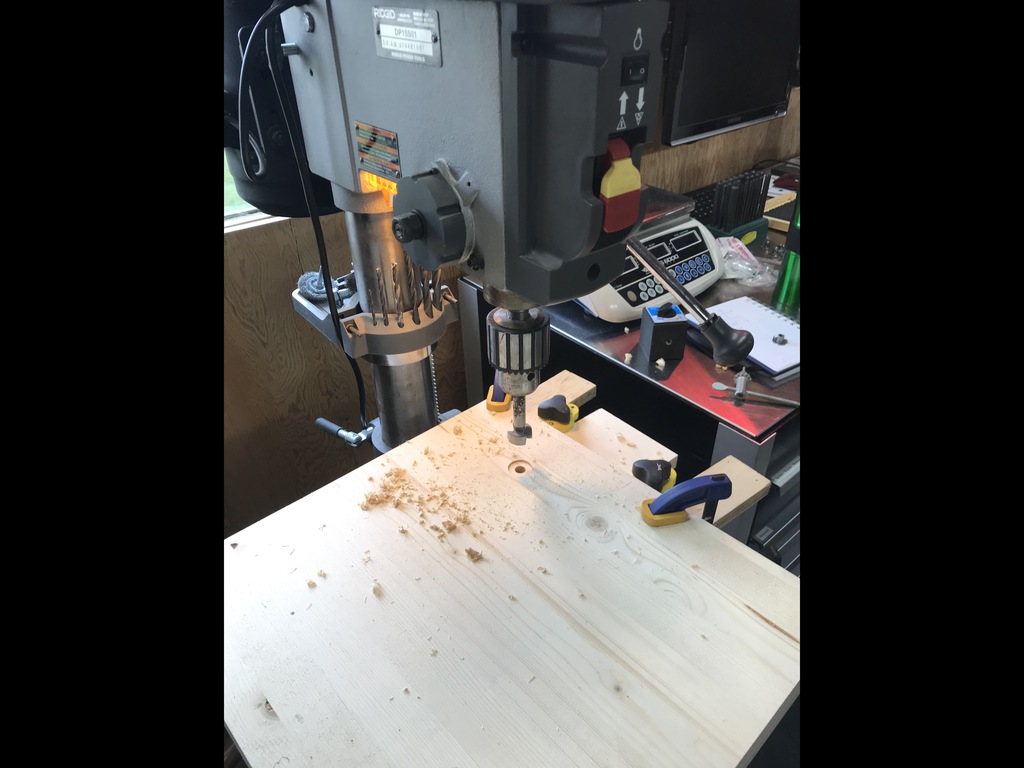
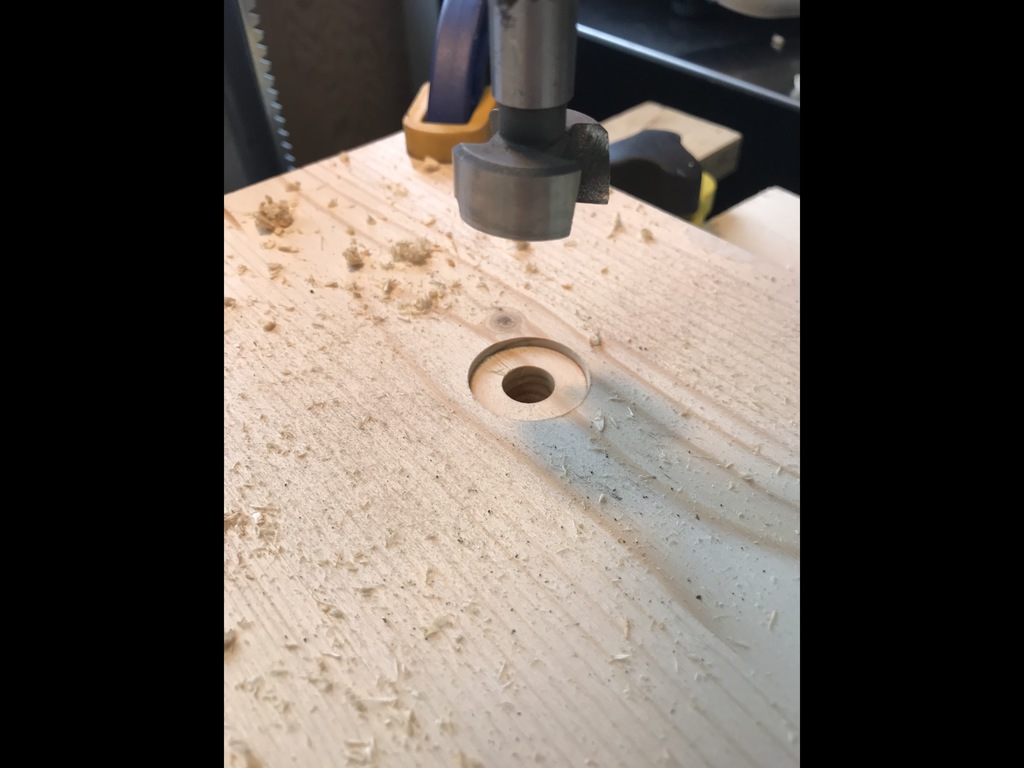
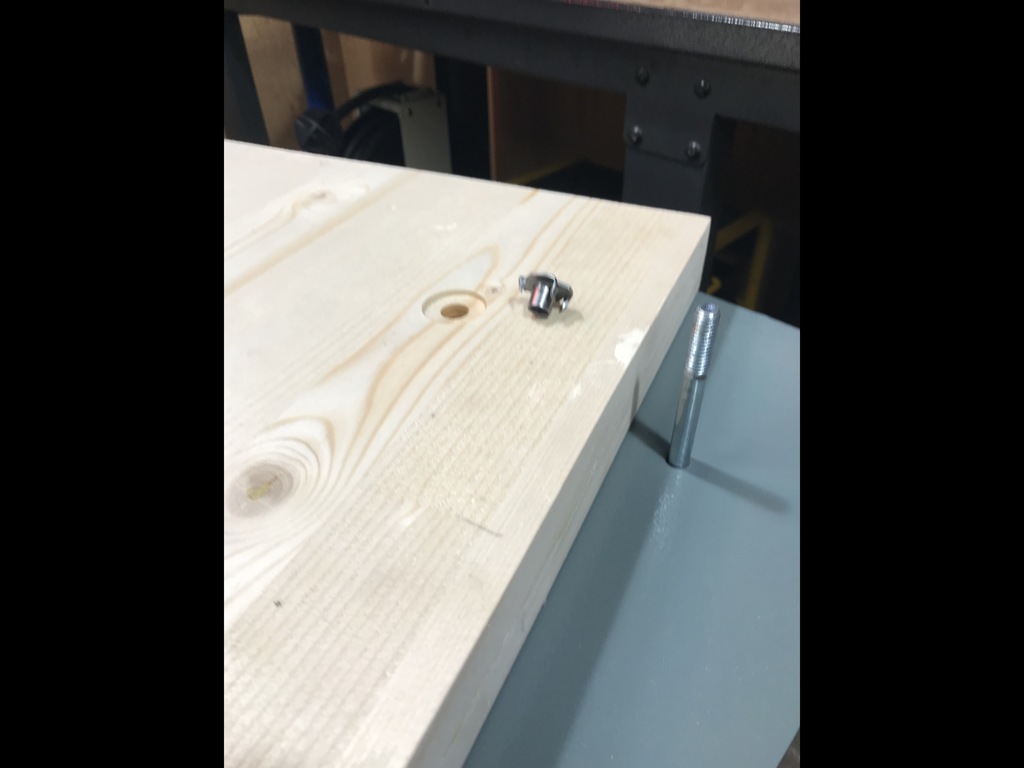
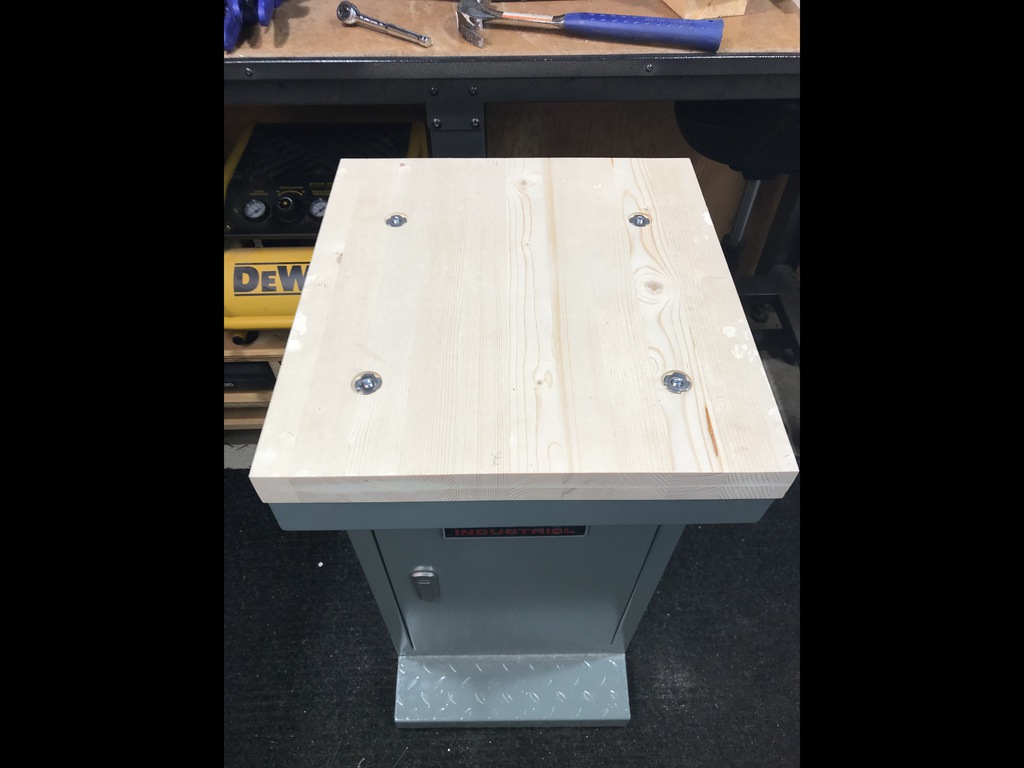
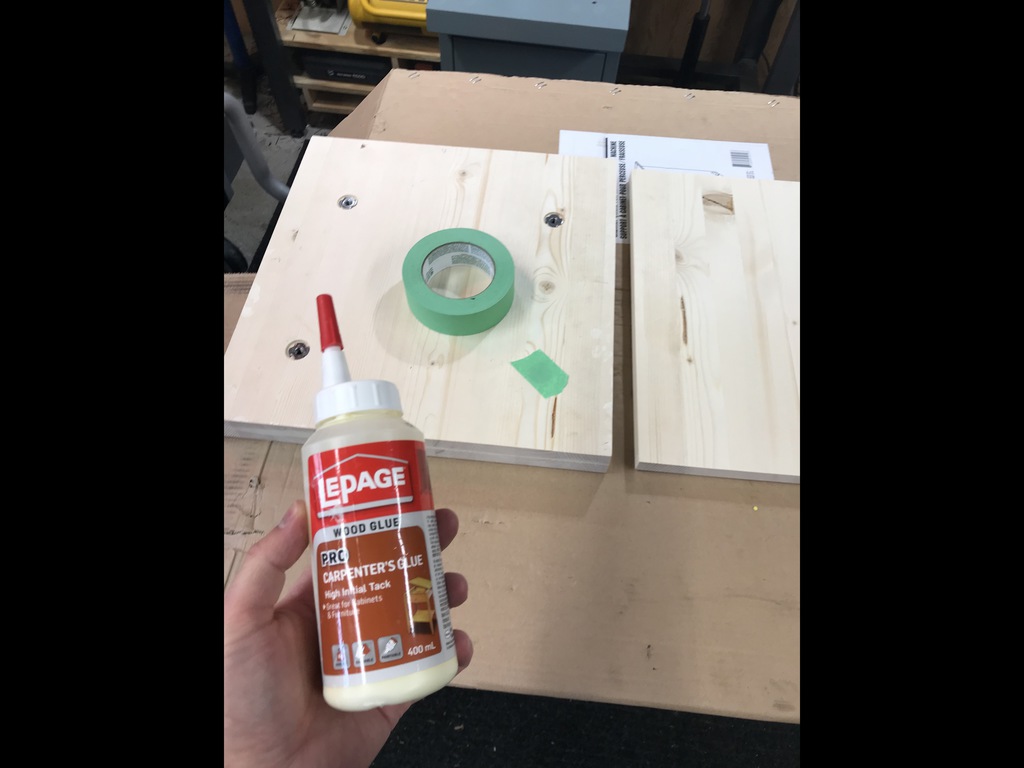
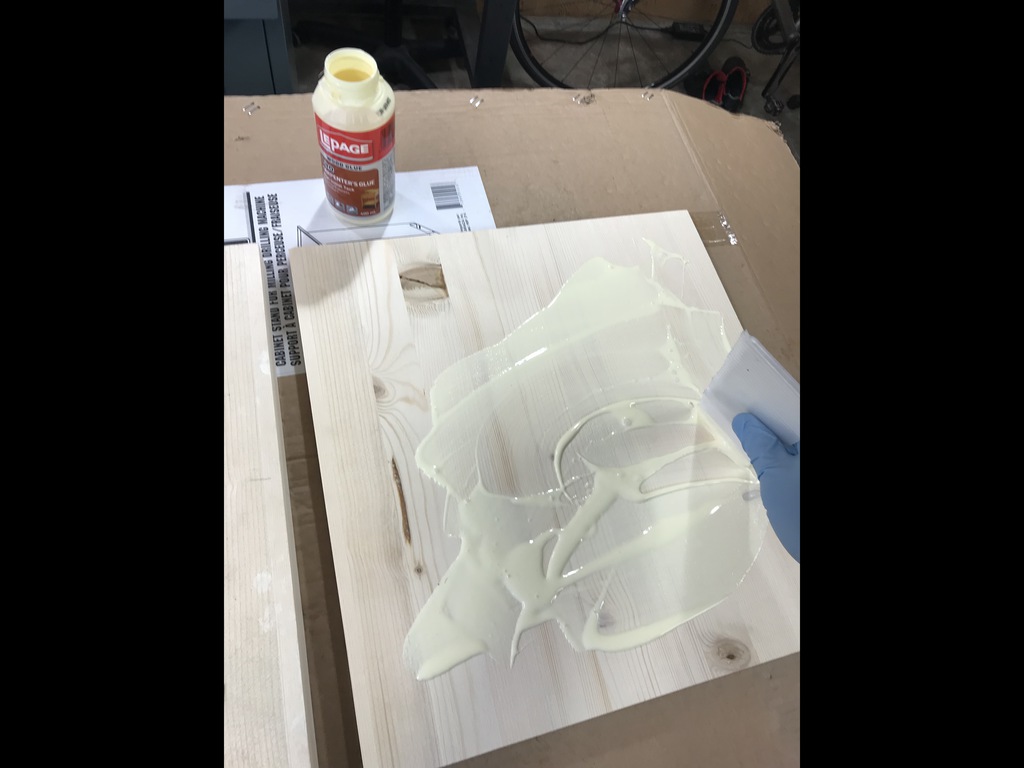
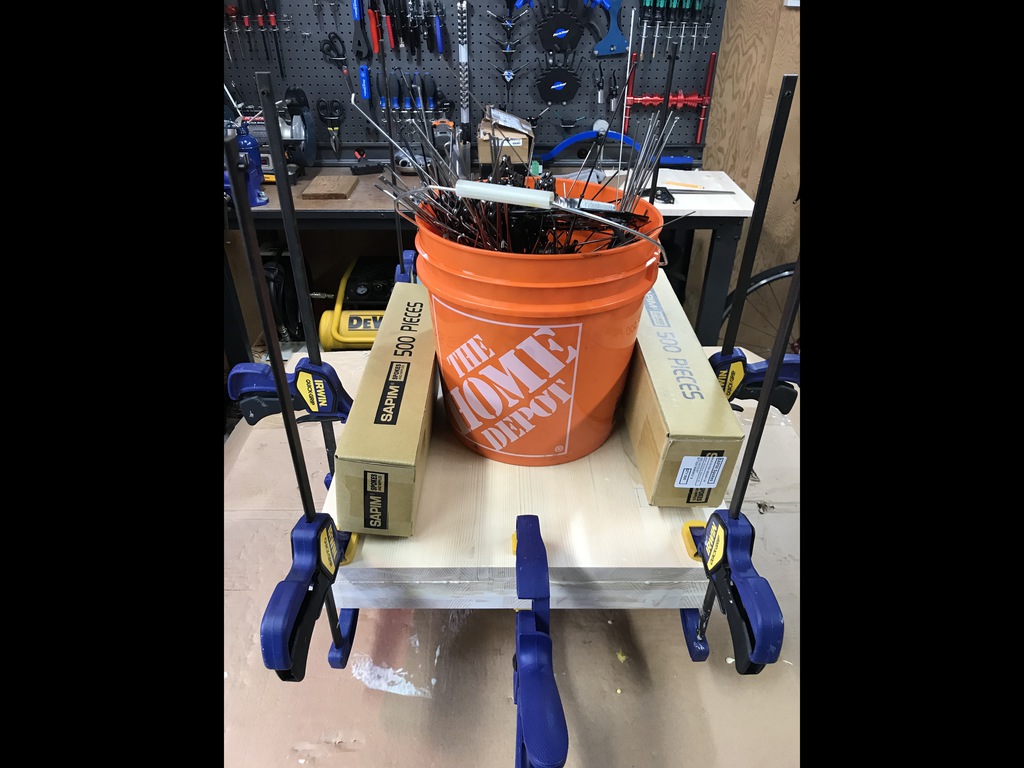
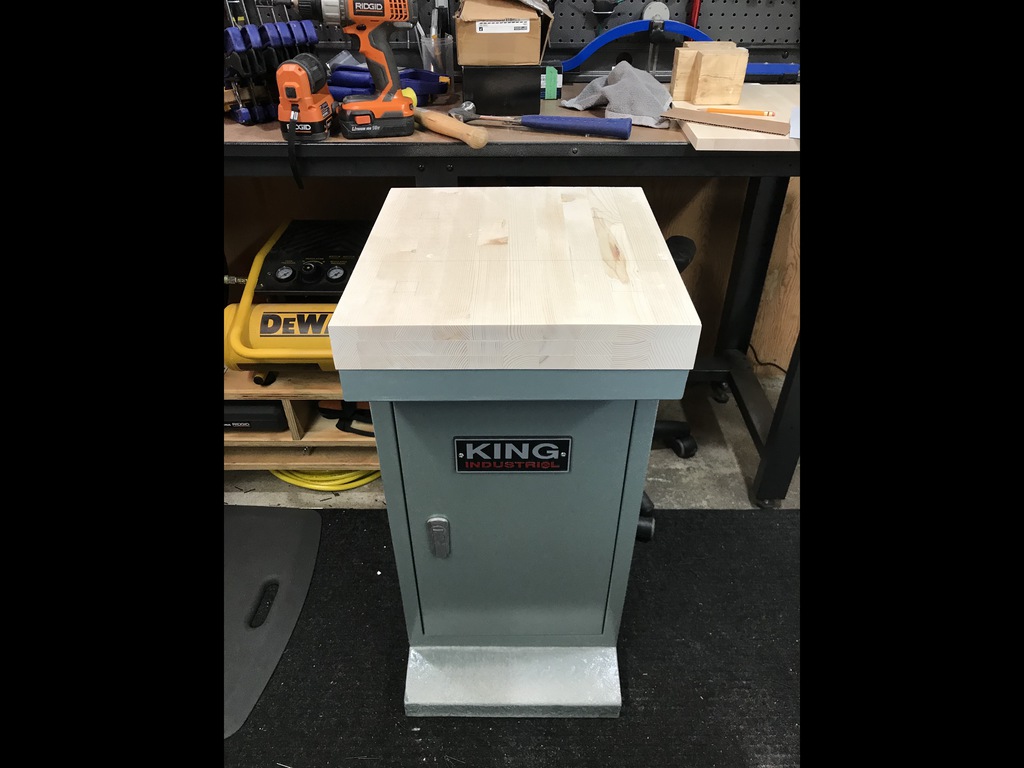
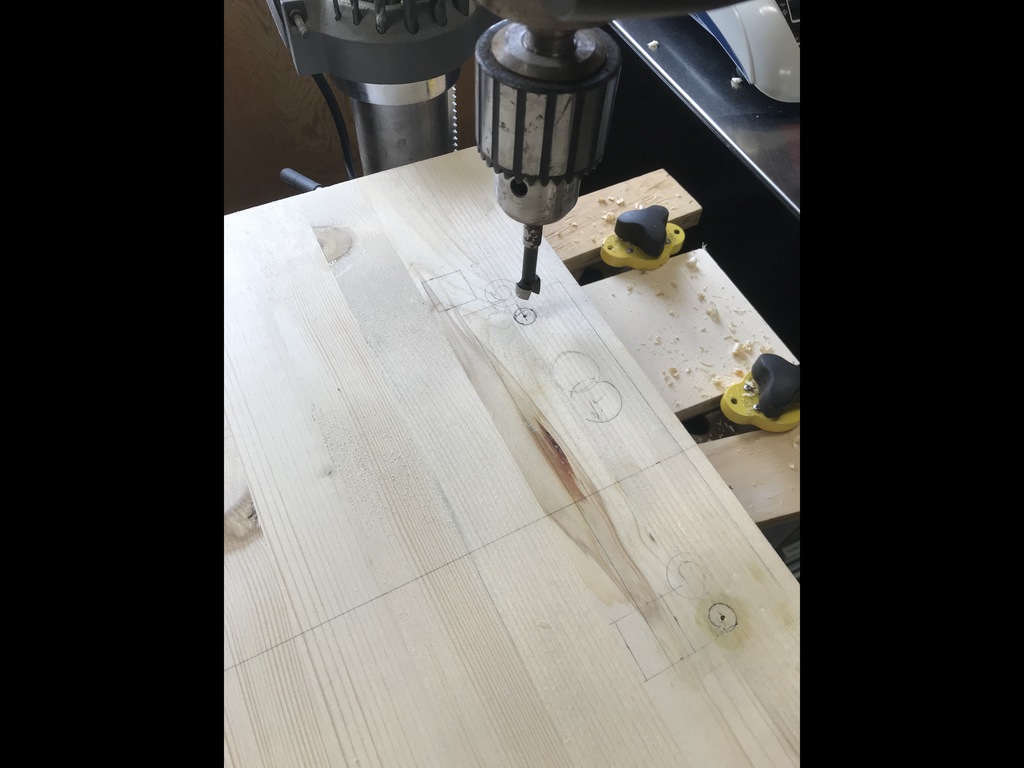
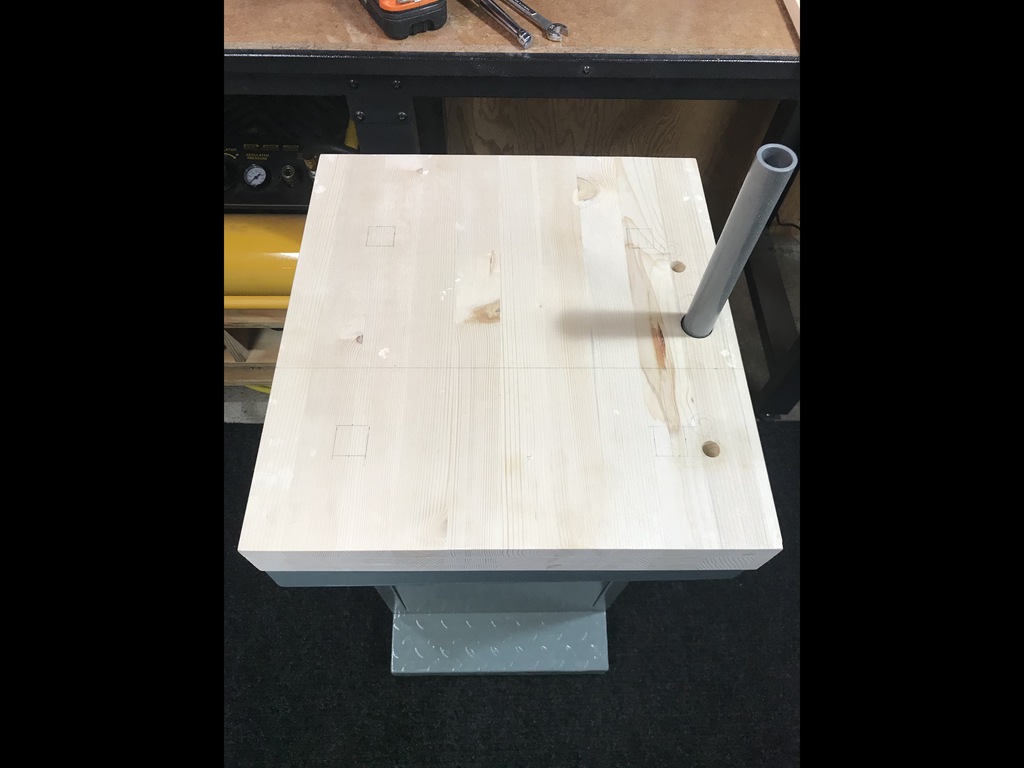
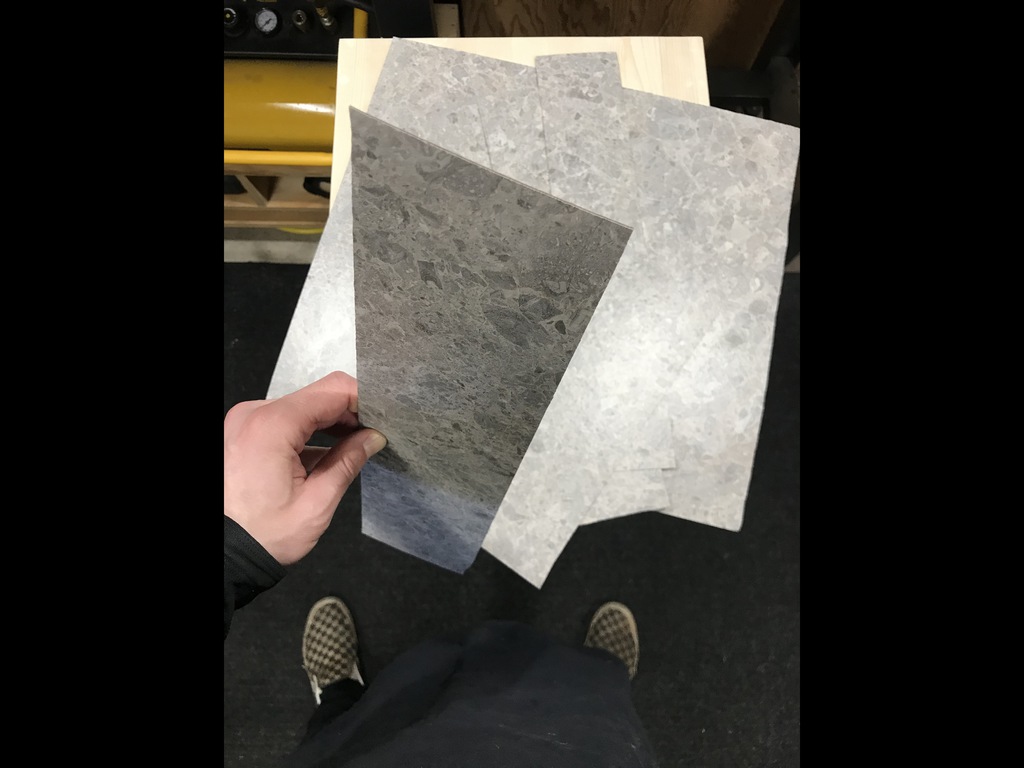
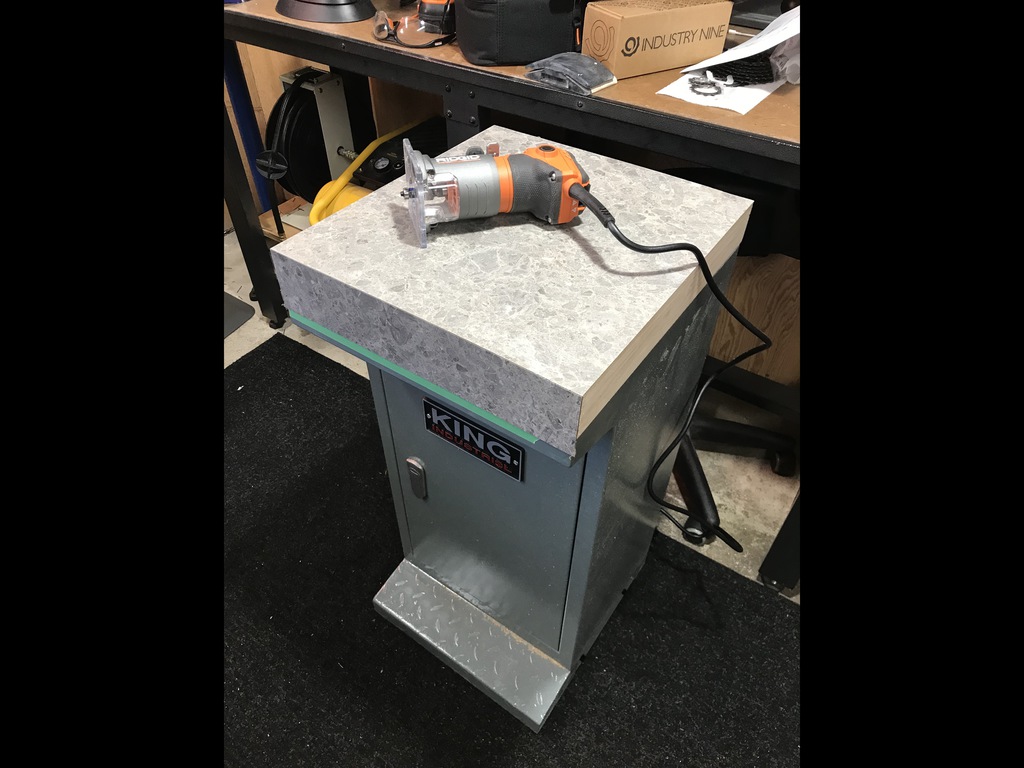
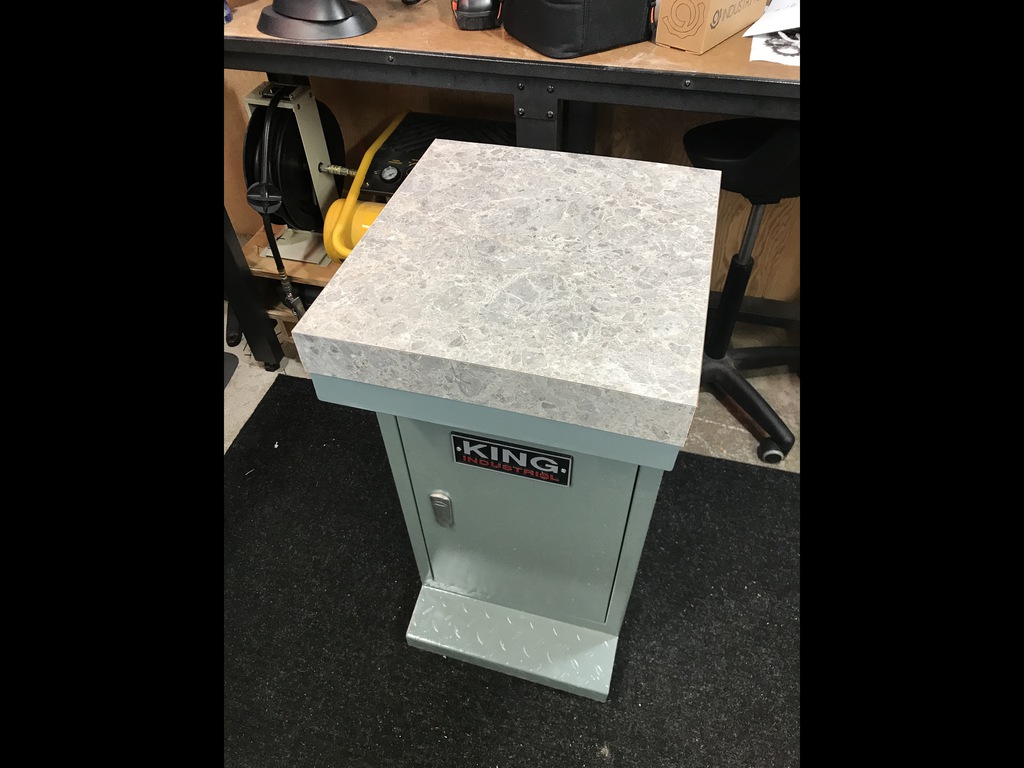
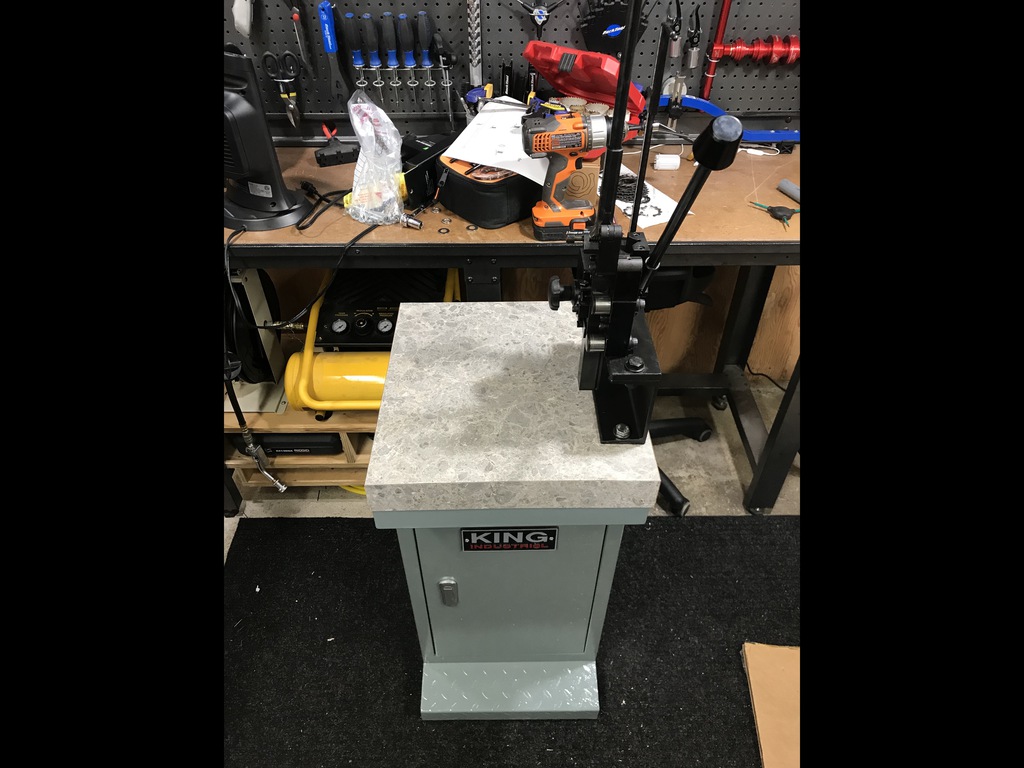